Introduction
An x-ray inspection system can be used to detect the stones, glass, ceramics, bones, plastics and, of course, metal, can be recognized and discharged with an x-ray inspection system which is more beneficial than Metal detectors that can only detect the metal especially ferrous metal.
The big advantage of x-ray inspection systems compared to metal detectors is that more types of contaminants
(other than metal) can be discovered. while processing in dairy and food industry.
Functional Principle of X-Ray Inspection Systems
An x-ray tube in its simplest form consists of a cathode and an anode inside a vacuum housed within a sealed glass or ceramic body.
The cathode emits electrons, which are accelerated toward the anode through high voltage and then penetrate the anode material.
As soon as the electrons meet the anode material, x-ray radiation is emitted. This releases heat and makes cooling necessary.
The product being tested is transported on a conveyor system that runs between the x-ray generator and the detector. X-rays produced by the x-ray tube penetrate the product being analyzed.
And depending on the thickness, density and chemical makeup of the product, x-rays are absorbed by the product in the process.
The remaining x-rays are captured by a detector consisting of a linear arrangement of photo diodes and converted into gray scale values practically line for line.
Contaminations that have a higher density than the product absorb more radiation and result in darker zones on the x-ray. Special computer programs analyze the x-ray and if contaminations are detected, the affected product is discharged.
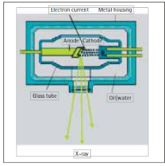
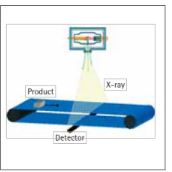
Detection Capability of X-Ray Inspection Systems
X-ray inspection is simply a matter of density determination. This means that only contaminations with a significantly higher density than that of the product can be detected. The following table illustrates some typical contaminations:
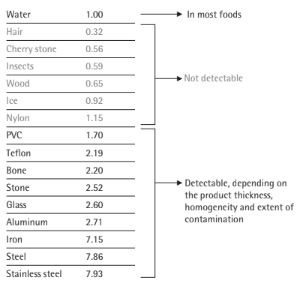
The thickness, homogeneity and density of the product play a decisive role here.
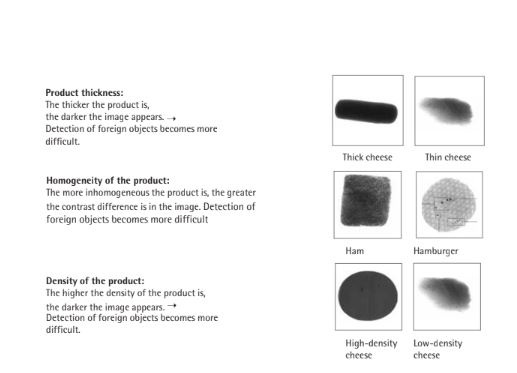
Advantages of using x-ray inspection systems
The big advantage of x-ray inspection systems compared to metal detectors is that more types of contaminants
(other than metal) can be discovered. In addition, it’s possible to detect metal contaminations even in metal
containers, metallic foils or in containers with metal closures.
Even products with a high product effect (such as a high salt and|or moisture content), which influences the sensitivity of conventional metal detectors, pose no problems for x-ray inspection systems.
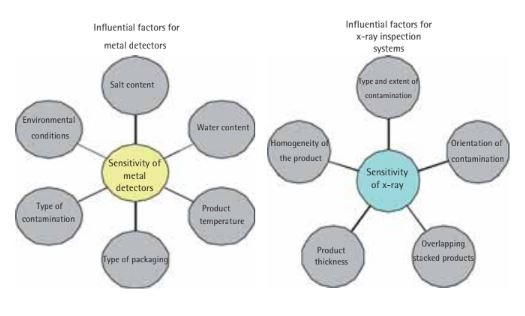
Additional Benefits of X-Ray Inspection Systems
In addition to the ability to clearly identify and discharge products with the most diverse contaminations, x-ray inspection technology also offers additional benefits, such as:
- Monitoring of form, volume and dimensions
- Monitoring of fill levels and quantities
- Completeness checks
- Weight monitoring
- Recognition of cavities and cracks within products
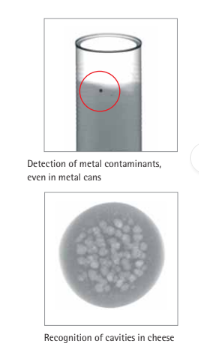
Types of X Ray Inspection system
Top/Down and Side Shooter-
The position of the x-ray tubes, the x-ray detector and the product influence the quality of the x-ray image significantly. Therefore, the most advantageous configuration allows the product to be penetrated by x-rays at the thinnest point and the contamination to be penetrated at the thickest point.
There are basically two different versions of the configuration. For flat, wide products, a configuration allowing the x-ray to penetrate the product from above or below (top/down hooter) is the most favorable.
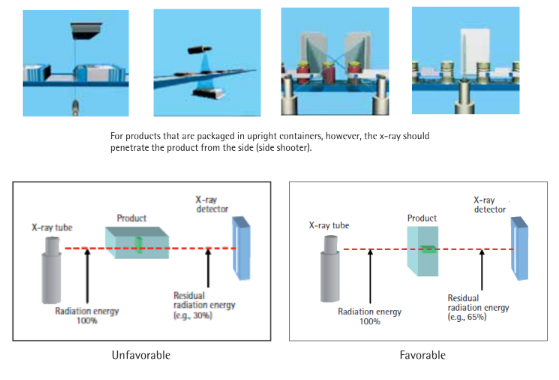
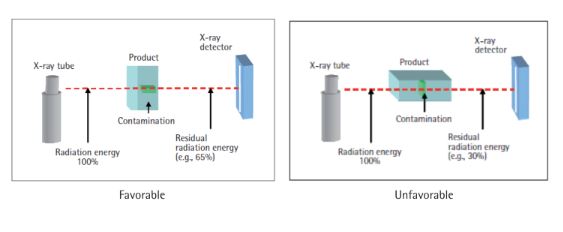
Single and Double Scanners
Contaminations located in curved areas of packages, on walls of containers or underneath caps or lids on drinks in jars, tin cans and bottles are especially challenging for any x-ray inspection system to detect.
This problem can be solved by using two x-ray tubes, which makes it possible to inspect the product from two sides.
Advantages of a double scanner system:
Shadows that appear in an x-ray image make it significantly more difficult to detect foreign objects. A double scanner system produces two views that are offset by 90°. This greatly improves the detection capability in especially critical areas.
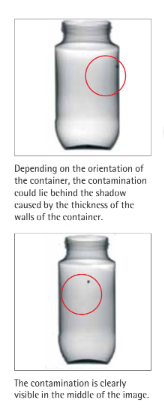
Summary and Conclusion
Increasing quality awareness has led to new laws, so that manufacturers are constantly faced with meeting new requirements in the production area. Special attention is being paid to the contamination of products. Foreign objects can enter the production process in a number of different ways.
In every case, however, these contaminants not only pose a hazard for the end user but could also damage processing machinery.
By using foreign object detection systems, such as x-ray inspection systems or metal detectors, contaminated products can be located and
safely discharged. This minimizes the risk to food and the likelihood of production downtimes and promotes consumer confidence as well.
By the same token, modern foreign object detection systems continue to fulfill requirements for transparency and traceability. In order to comply with particular requirements and maintain an optimum cost- benefit ratio, careful selection of a foreign object detection system is essential.